Welding Equipment in Automotive Shops: Essential Tools for Vehicle Repair and Restoration
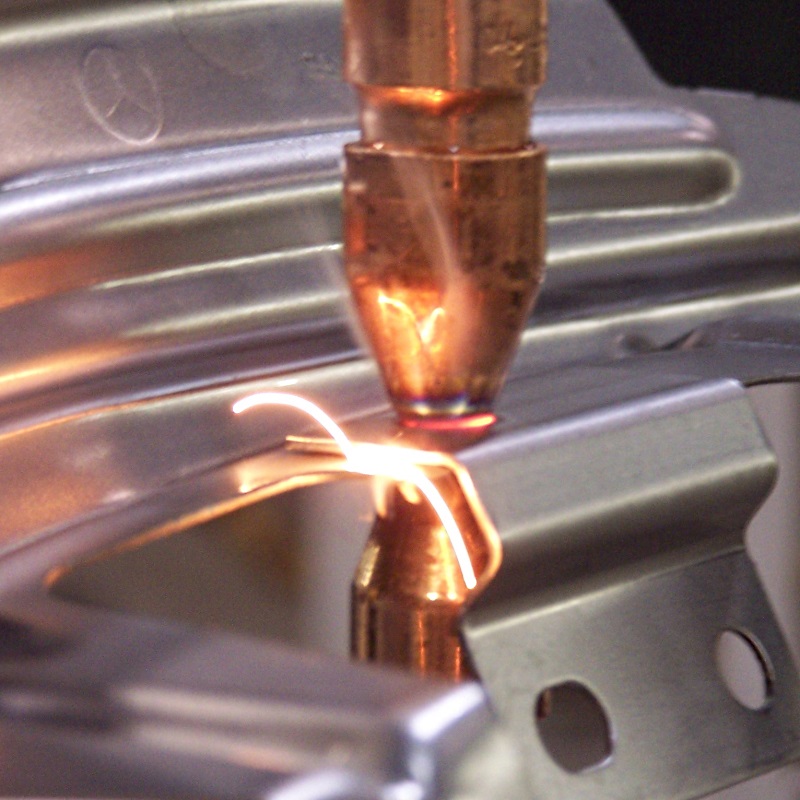
Understanding welding equipment in automotive repair
Welding play a crucial role in automotive repair and restoration. From fix damage frames to fabricate custom parts, the right welding equipment make all the difference in the quality and durability of repairs. Automotive shops utilize various specialized welding tools design to handle the unique challenges of vehicle metalwork.
Unlike general welding applications, automotive welding oftentimes require work with thin gauge metals, specialized alloys, and in tight spaces. This demand equipment that offer precision, versatility, and appropriate power settings to prevent warping or burn through materials.

Source: theweldingmaster.com
MIG welders: the automotive shop workhorse
Metal inert gas (mMIG)welders stand as the nigh common welding equipment find in automotive repair facilities. These welders use a anncessantly feed wire electrode and a shielding gas to create strong, clean welds that are ideal for automotive applications.
The popularity of MIG welders in automotive shops stem from several key advantages:
-
Versatility
Capable of weld various metals include mild steel, stainless steel, and aluminum -
Speed
Allows for faster welding compare to other methods, improve shop efficiency -
Clean welds
Produce minimal spatter and slag, reduce post weld cleanup time -
Ease of use
Require less training to achieve acceptable results compare to TIG welding -
Adjustable settings
Modern units offer precise control over wire feed speed and voltage
Professional automotive shops typically invest in 220 volt MIG welders with output ranges between 30 200 amps. This power range provides the flexibility to work on everything from thin body panels to thicker frame components. Many modernMIGg welders too feature dual voltage capabilities( 110v/220v), allow shops to adapt to different power supply situations.
MIG welder accessories for automotive applications
Beyond the base unit, automotive MIG welding setups include several specialized components:
-
Wire feed systems
Quality drive rollers ensure consistent wire feeding for smooth welds -
Multiple gun tips
Different sizes accommodate various material thicknesses -
Gas regulators
Precise control of shielding gas flow for optimal weld protection -
Spool guns
Specialized attachments for aluminum welding that prevent wire feeding issues
Many automotive shops opt for MIG welders with pulse capabilities, which deliver control bursts of power. This feature help when weld thin auto body panels, reduce the risk of burn through while maintain adequate penetration.
TIG welders: precision for specialty work
Tungsten inert gas (tTIG)welders represent the pinnacle of precision in automotive welding. While require more skill to master, tiTIGelding deliver unmatched results for certain automotive applications.
Automotive shops utilize TIG welders mainly for:
-
Aluminum components
Especially for custom fabrication or repair aluminum body panels -
Thin gauge metals
When work with delicate sheet metal that could well burn through -
Stainless steel exhaust systems
Create clean, durable connections in performance exhaust fabrication -
Restoration projects
When appearance matter equally often as structural integrity -
Custom fabrication
Create one off parts that require superior finish quality
Professional automotive TIG welders typically feature ac / DC functionality, allow them to work with both aluminum (ac )and steel ( ( DC)dvanced models include foot pedals for amperage control, which give welders precise heat management during the welding process — critical when work on thin automotive metals.
TIG welder components for automotive applications
A complete TIG setup in an automotive shop include:
-
Various tungsten electrode size
Typically range from 1/16″ to 3/32 ” or automotive work -
Assorted ceramic cups
Different diameters to control gas coverage area -
Filler rods
Various alloys select to match the base metals being welded -
Gas lenses
For improved gas coverage in tight or awkward positions -
Flexible gas hoses
Allow access too difficult to reach areas in vehicle structures
High-end automotive shops oft invest in TIG welders with programmable memory settings. These allow technicians to save optimal parameters for different materials and thicknesses, ensure consistency across multiple repair jobs.
Spot welders: essential for body panel work
Spot welders serve a specific but critical function in automotive repair shops. These specialized machines recreate factory spot welds when replace body panels, ensure structural integrity equivalent to original manufacturer specifications.
Modern automotive spot welders feature:
-
Microprocessor control
Mechanically adjust current and weld time base on material thickness -
Water cool systems
Prevent overheating during consecutive spot welds -
Multiple welding arms
Different configurations to access various areas of the vehicle -
Pressure monitoring
Ensures consistent clamp force for reliable weld quality -
Weld quality testing
Some advanced units can test spot weld strength
Professional body shops typically use single phase 220v spot welders with output capabilities range from 8,000 13,000 amps. This power range allows them to efficaciously join the high strength steels progressively common in modern vehicle construction.
Spot welder adaptability for modern vehicles
As vehicle construction evolve, hence besides must spot welding equipment. Today’s automotive spot welders come with specialized programs for:
-
High strength steel (hHSS)
Require precise heat control to maintain material properties -
Ultra-high strength steel ( uh( HSS)
Demand specific welding parameters to achieve proper fusion -
Boron steel
Necessitating higher current and shorter weld times -
Aluminum components
Require specialized settings for proper joint formation
Many automotive manufacturers directly specify exact spot weld parameters for collision repairs, make programmable spot welders essential for shops seek manufacturer certification.
Plasma cutters: precision cutting tools
While not weld equipment per se, plasma cutters often accompany weld setups in automotive shops. These tools use a high velocity jet of ionized gas to cut through metal with remarkable precision.
Automotive technicians rely on plasma cutters for:
-
Remove damage sections
Flawlessly cut out compromise metal before repairs -
Fabricate replacement panels
Create custom pieces when pre make parts aren’t available -
Custom modifications
Incisively shape metal for performance or aesthetic enhancements -
Rust repair
Remove corrode sections with minimal damage to surround metal
Professional automotive plasma cutters typically offer cut capacities between 1/4″ to 1/2 ” hickness, more than adequate for most vehicle metals. Many modern units feature pilot arc technology, which allow cut through paint or rusty surfaces without direct contact — ideal for automotive restoration work.
Plasma cutter accessories for automotive work
A complete plasma cutting station in an automotive shop includes:
-
Circle cut attachments
for creating precise circular cuts -
Edge guide
Ensure straight cuts along predetermine lines -
Multiple nozzle sizes
Different diameters for various cutting applications -
Air filtration systems
Remove moisture from compressed air to extend consumable life -
CNC interfaces
In advanced shops, allow computer control cutting for complex shapes
Many automotive shops directly opt for 3 in 1 or multiprocess machines that combine plasma cutting with mMIGand sometimes tTIGwelding capabilities, maximize utility while minimize shop space requirements.
Specialized welding equipment for aluminum
With the increase use of aluminum in modern vehicles, automotive shops have invested in specialized equipment design specifically for this challenging metal.
Aluminum focus welding equipment include:
-
Pulse MIG welders
Deliver control power pulses that reduce heat input -
Push-pull wire feed systems
Prevent the soft aluminum wire from bind in the feed line -
Dedicated spool guns
Keep the aluminum wire feed path short to prevent feeding issues -
Specialized cleaning tools
Remove the oxide layer that complicate aluminum welding
High-end automotive shops work oftentimes with aluminum oftentimes maintain separate welding stations solely for aluminum work. This prevents cross contamination issues that can compromise weld quality.
Safety equipment for automotive welding
Professional automotive shops maintain comprehensive safety equipment alongside their welding tools. These safety components are not optional but essential for proper operation.
Standard weld safety equipment include:

Source: Korean machinery.com
-
Auto darken helmets
With adjustable shade settings for different welding processes -
Flame resistant clothing
Protect against sparks and spatter -
Welding gloves
heat-resistant and offer adequate dexterity -
Fume extraction systems
Remove harmful welding gases and particulates -
Fire suppression equipment
Promptly accessible in case of emergencies -
Welding screens
Protect other shop personnel from arc flash exposure
Many automotive shops besides invest in specialized welding tables with integrate ventilation systems. These tables capture fumes from beneath while provide a stable, fire-resistant work surface.
Welding equipment maintenance in automotive shops
Professional automotive shops implement regular maintenance protocols for their welding equipment to ensure consistent performance and longevity.
Typical maintenance procedures include:
-
Daily inspection of cables and connections
Check for wear or damage -
Regular cleaning of wire feed mechanisms
Prevent feed issues that compromise weld quality -
Replacement of consumables
Maintain fresh contact tips, nozzles, and electrodes -
Gas system leak tests
Ensure proper shielding gas delivery and prevent waste -
Cool system maintenance
For water cool equipment like spot welders
Many shops maintain detailed maintenance logs for each piece of welding equipment, track consumable usage and schedule service intervals. This documentation oftentimes supports warranty claims and helps identify equipment near the end of its service life.
Emerging welding technologies in automotive repair
The automotive repair industry continues to evolve with new welding technologies design to address the challenges of modern vehicle construction.
Recent innovations include:
-
Cold metal transfer (cCMT)
A modify MIG process that reduce heat input, ideal for thin materials -
Resistance spot weld with adhesive
Combine traditional spot weld with structural adhesives for enhanced strength -
Laser welding systems
Become more accessible for high-end shops work on luxury vehicles -
Ultrasonic welding
For join dissimilar materials include certain plastics to metals -
Smart welding systems
Equipment that mechanically adjust parameters base on material detection
Forward think automotive shops progressively invest in training for these advanced technologies, recognize that stay current with welding innovations direct impact their ability to right repair newer vehicles.
Selecting welding equipment for an automotive shop
For shop owners and managers, choose the right welding equipment represent a significant business decision. The selection process typically considers several key factors:
-
Types of vehicles service
Different make require different welding capabilities -
Manufacturer certifications
Many require specific equipment to maintain certification -
Budget constraint
Balance initial cost against long term performance -
Space limitations
Consider the physical footprint of the equipment -
Staff expertise
Match equipment complexity to technician skill levels -
Future need
Anticipate evolve vehicle construction techniques
Many automotive shops develop relationships with welding equipment suppliers who can provide ongoing support, training, and maintenance. These partnerships oftentimes prove valuable when troubleshooting issues or upgrade equipment as need change.
Conclusion
The welding equipment find in modern automotive shops represent a sophisticated array of specialized tools, each design to address specific repair challenges. From versatile MIG welders to precision TIG systems, powerful spot welders, and complementary plasma cutters, these machines form the backbone of structural repair capabilities.
As vehicle construction continue to evolve — incorporate more aluminum, high strength steels, and mixed materials — weld equipment manufacturers respond with progressively advanced technologies. For automotive repair professionals, stay current with these developments ensure the ability to restore vehicles to their pre accident condition while maintain structural integrity.
Understand the capabilities and limitations of automotive welding equipment help shop owners make informed investment decisions while give customers confidence in the quality and safety of repairs perform. In the hands of skilled technicians, these specialized tools transform damage vehicles into roadworthy transportation, oft with no visible evidence of the repair process.