Automotive Sheet Metal Thickness: Complete Guide for Car Enthusiasts
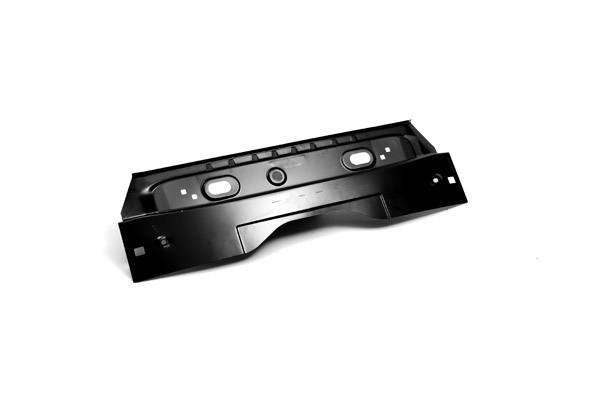
Understand automotive sheet metal thickness
Automotive sheet metal thickness vary importantly depend on the vehicle part, manufacturer specifications, and intend purpose. Most modern vehicles use sheet metal range from 0.7 mm to 2.0 mm thick, with specific applications require different gauges to balance strength, weight, and formability.
Standard thickness measurements for vehicle body panels
When discuss automotive sheet metal thickness, manufacturers typically use either the metric system (millimeters )or gauge numbers. The lower the gauge number, the thicker the metal. Here’s a breakdown of common automotive sheet metal thicknesses:
Exterior body panels
Most exterior body panels on modern vehicles use sheet metal with these specifications:
- Hood: 0.8 mm to 1.0 mm (20 22 gauge )
- Doors: 0.7 mm to 0.9 mm (22 24 gauge )
- Fenders: 0.7 mm to 0.8 mm (22 24 gauge )
- Roof: 0.7 mm to 0.9 mm (22 24 gauge )
- Trunk / lift gate: 0.8 mm to 1.0 mm( 20 22 gauge)
Structural components
Structural elements that contribute to the vehicle’s rigidity and crash safety use thicker metal:
- Frame rails: 1.5 mm to 2.0 mm (16 18 gauge )
-
Pillars (a, b, c ) 1.2 mm to 1.8 mm ( ( 19 gauge )
) - Rocker panels: 1.2 mm to 1.6 mm (16 18 gauge )
- Firewall: 1.0 mm to 1.5 mm (18 20 gauge )
- Floor pans: 0.9 mm to 1.2 mm (19 22 gauge )
How material selection affects thickness requirements
The type of metal use importantly impact the requirement thickness for automotive applications. Different materials offer vary levels of strength, formability, and corrosion resistance.
Steel variants
Steel remain the nearly common material for automotive sheet metal, but several variants exist:
-
Mild steel:
Traditional choice, typically 0.8 1.0 mm thick for body panels. Offer good formability but require greater thickness for structural strength. -
High strength steel (hHSS)
Can be 10 15 % thinner than mild steel while maintain equivalent strength. Usually use in structural components. -
Advanced high strength steel (aAHS))
Allow for regular thinner applications (0.6 0.8 mm )while provide superior strength. Use in safety critical areas. -
Ultra-high strength steel ( uh( HSS )
Use in key structural components at 1.0 1.5 mm thickness, provide exceptional crash resistance.
Aluminum
Aluminum body panels are become progressively common in modern vehicles:

Source: sizepedia.org
- Typically, 25 30 % thicker than steel equivalents( 1.0 1.2 mm) to achieve comparable strength
- Despite increase thickness, aluminum components weigh 40 60 % less than steel counterparts
- Premium and performance vehicles oft use aluminum hoods and doors at 1.0 1.5 mm thickness
Historical changes in automotive sheet metal thickness
The thickness of automotive sheet metal has evolved importantly over the decades:
Classic cars (1950s 1970s )
Vehicles from this era feature considerably thicker sheet metal:
- Body panels: 1.0 1.2 mm (18 20 gauge )
- Structural components: 1.5 2.5 mm (14 16 gauge )
- Limited use of high strength materials mean thicker metal was necessary for structural integrity
- These thicker panels contribute to the solid feel of classic cars but add significant weight
Modern manufacturing (1990s present )
Contemporary vehicles use thinner however stronger materials:
- Advanced metallurgy allow for thinner panels (0.7 0.9 mm )without compromise strength
- Computer design crumple zones and strategic reinforcement have replaced the need for uniform thickness
- Weight reduction efforts have driven the trend toward optimize thickness in specific areas
Why thickness vary across vehicle models
Not all vehicles use the same thickness of sheet metal, with variations base on:
Vehicle class and price point
-
Economy cars:
Oft use the minimum viable thickness (0.7 0.8 mm )for nonon-structuralanels to reduce costs -
Luxury vehicles:
May use slender thicker panels ( (9 1.0 mm ) )r improve dent resistance and perceive quality -
Performance cars:
Often employ thinner, lighter materials with advanced alloys or aluminum construction -
Trucks and SUVs:
Typically, feature thicker body panels( 0.9 1.1 mm) for increase durability in demand conditions
Regional manufacturing differences
Sheet metal thickness can vary by market and manufacturing location:
- European manufacturers oft use thinner, higher strength steels (0.7 0.8 mm )
-
American vehicles traditionally use slender thicker panels ( (8 1.0 mm )
) - Japanese and Korean manufacturers typically fall in the middle range (0.7 0.9 mm )
Impact of sheet metal thickness on vehicle performance
The thickness of automotive sheet metal flat affect several aspects of vehicle performance:
Weight and fuel economy
Thinner sheet metal contribute to lighter vehicles:
- Reduce body panel thickness by 0.1 mm can save 5 10 kg across an entire vehicle
- Each 10 % reduction in vehicle weight typically improve fuel economy by 6 8 %
- Modern vehicles use variable thickness strategies to reduce weight in non-critical areas
Safety considerations
Despite thinner panels, modern vehicles are safer due to strategic design:
- Critical structural components maintain adequate thickness (1.2 2.0 mm )for crash protection
- Advanced high strength steels allow for thinner however stronger crash structures
- Crumple zones use cautiously calibrate material thickness to absorb impact energy
- Safety cages around passenger compartments use the thickest materials (1.5 2.0 mm )
Durability and dent resistance
Thinner panels can affect everyday durability:
- Modern 0.7 mm body panels are more susceptible to dents from minor impacts
- High strength steel improve dent resistance despite reduced thickness
- Some manufacturers use reinforce double layer construction in vulnerable areas
Sheet metal thickness for DIY repairs and restoration
When perform repairs or restoration work, match the correct sheet metal thickness is crucial:
Replacement panel selection
For DIY repairs, consider these guidelines:
- Use a micrometer to measure the thickness of the original panel when possible
- For classic car restoration, 18 20 gauge (1.0 1.2 mm )sheet metal is typically appropriate for body panels
- Modern vehicle repairs should match OEM specifications (normally 0.7 0.9 mm for exterior panels )
- Structural repairs should invariably use the exact specify gauge or thickness
Aftermarket considerations
When purchase aftermarket panels:
- Quality replacement panels should match OEM thickness specifications
- Budget panels may use thinner material (0.6 0.7 mm )that’s more prone to dent
- Some performance applications benefit from upgrade to slender thicker material
- Remember that thicker isn’t invariably better — modern vehicles are design for specific thicknesses
Advanced manufacturing techniques and variable thickness
Modern vehicles seldom use uniform sheet metal thickness throughout their construction:
Tailor weld blanks
This advanced manufacturing technique allows for variable thickness within a single panel:
- Different thicknesses of sheet metal are laser weld unitedly before stamp
-
Allow reinforcement exclusively where need (1.0 1.5 mm )while keep other areas thinner ( (7 0.9 mm )
) - Optimize the strength to weight ratio across complex components
Hot form steel components
Some modern structural components use advanced processing:

Source: mingy an metal.com
- Sheet metal is heat to roughly 900 ° c before form
- Rapid cooling in the die create ultra-high strength properties
- Allow for thinner material (1.0 1.2 mm )with strength equivalent to practically thicker conventional steel
- Usually use in safety critical areas like b pillars and door intrusion beams
Measure sheet metal thickness
For those work with automotive sheet metal, accurate measurement is essential:
Tools for thickness measurement
-
Micrometer:
The nigh accurate tool for measure sheet metal thickness, provide readings to 0.01 mm -
Ultrasonic thickness gauge:
Non-destructive tool that can measure thickness without access both sides of the metal -
Sheet metal gauge:
Traditional tool with notches correspond to standard gauge sizes
Convert between measurement systems
Understand the relationship between different measurement systems is helpful:
- 18 gauge = roughly 1.2 mm
- 20 gauge = roughly 0.9 mm
- 22 gauge = roughly 0.8 mm
- 24 gauge = roughly 0.6 mm
Future trends in automotive sheet metal
The automotive industry continues to evolve its approach to sheet metal:
Multi material construction
Future vehicles progressively use mixed materials:
- Strategic use of aluminum (1.0 1.5 mm )for hoods, doors, and fenders
- Advanced high strength steel (0.7 1.2 mm )for structural components
- Carbon fiber reinforce polymers for specialized applications
- Each material select for optimal thickness to strength ratio in specific locations
Continue optimization
Manufacturers continue to refine sheet metal usage:
- Computer simulation allow for precise thickness optimization
- Some non-critical panels may become yet thinner (0.6 0.7 mm )as material science advance
- Structural components benefit from ultra-high strength materials at optimize thicknesses
Conclusion
Automotive sheet metal thickness represent a careful balance between strength, weight, manufacturability, and cost. While classic vehicles use comparatively thick, uniform sheet metal, modern vehicles employ a sophisticated approach with variable thickness and advanced materials. Understand these specifications is crucial for proper repairs, restorations, and appreciate the engineering behind vehicle design.
For DIY enthusiasts and professionals similar, match the correct sheet metal thickness is essential for maintaining structural integrity and ensure proper fit and finish. As automotive technology continue to advance, we can expect further refinements in how manufacturers utilize sheet metal thickness to create vehicles that are simultaneously lighter, stronger, and more efficient.